Jim O'Brien
The classic design of the Shakers has always intrigued me, and I am compelled by the spare and graceful quality of their aesthetic
I consider myself a craftsman of necessity. There was a time when, if I wanted nice things, I had to make them for myself. I found that I enjoyed woodworking immensely, and stayed with it long after I could afford what I wanted.
Without formal artistic training, I have occasionally taken classes through the years and looked over the shoulder of those with more skill and experience in order to develop my own. I work primarily by hand, using machinery only when it makes sense. I have a large set of working hand tools dating from the 18th century to WWI. My operation resembles a turn-of-the-century cabinetmaker’s shop. All of my work is hand fit and finished.
The classic design of the Shakers has always intrigued me, and I am compelled by the spare and graceful quality of their aesthetic. It is deceptively simple in appearance, remarkably frugal, and ingenious. Making quality examples of their work demands full attention to detail in material choice, construction, joinery, and finish.
Pantry boxes were commonly used for storage in 19th century homes and the Shakers distinguished themselves with the development of the oval box with finger joints. They were used for storing spices, dry goods, sewing supplies, and many other household items.
With materials in hand, making an oval box takes 2-3 days from start to finish. I start with feathering the ends of the veneer bands, drilling pilot holes, and cutting the finger joints. The bands are poached in hot water to facilitate bending. After softening, they are pulled from the water, then bent and held around an oval mold. Once the shape begins to set, the copper tacks are hammered in place over a small anvil, and the piece is left to dry overnight with oval plugs to hold the shape.
On the second day, the top and bottom pieces are traced, cut, and fit to size. Wooden pegs are then inserted in holes around the edge to hold the pieces in place and trimmed flush. No glue is used in construction. After all the rough spots are cleaned up, a coat of linseed oil is applied and left to dry overnight. On the third day, I give the box several coats of shellac and finish with a coat of wax.
All materials are sourced from local and Michigan suppliers. I get my wood from local mills and building supply stores. I slice my own veneers or have them milled locally. Even the copper tacks are manufactured in Michigan. My shop is in the basement of my home in Hubbell in the Western UP.
Jim O’Brien was born in Detroit and moved to the Copper Country at a young age. One of 11 children of a social worker and an artist, he grew up with strong aesthetic influences. His father sang in community and church choirs for over 60 years and his mother was an interior designer.
Like all of his siblings, he has pursued a career, or an avocation in the arts. In addition to his work in woodcraft, he has also been active in music and theater since childhood. He picked up his interest in woodworking while renovating the home in Hubbell that he and his wife Cheryl have lived in for over 40 years. He is an avid antique tool collector and prefers to work by hand when possible
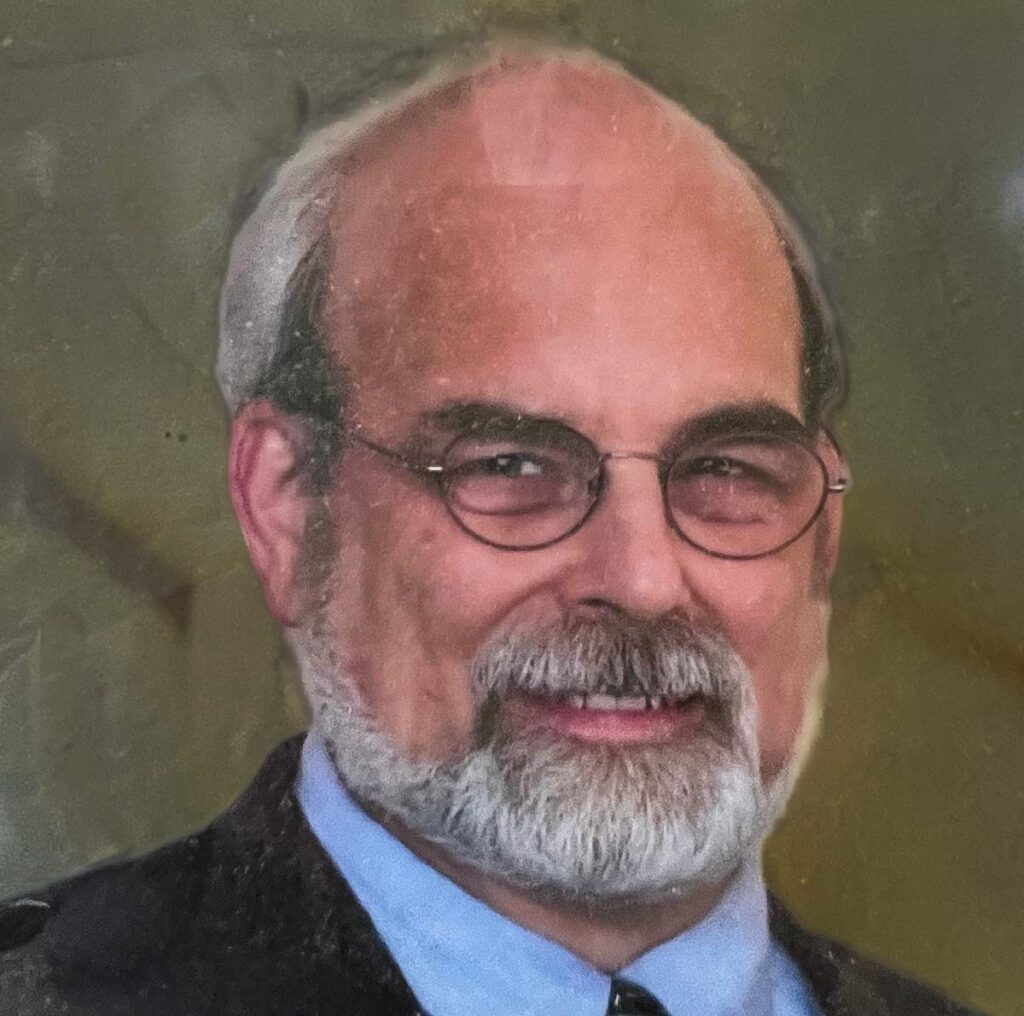
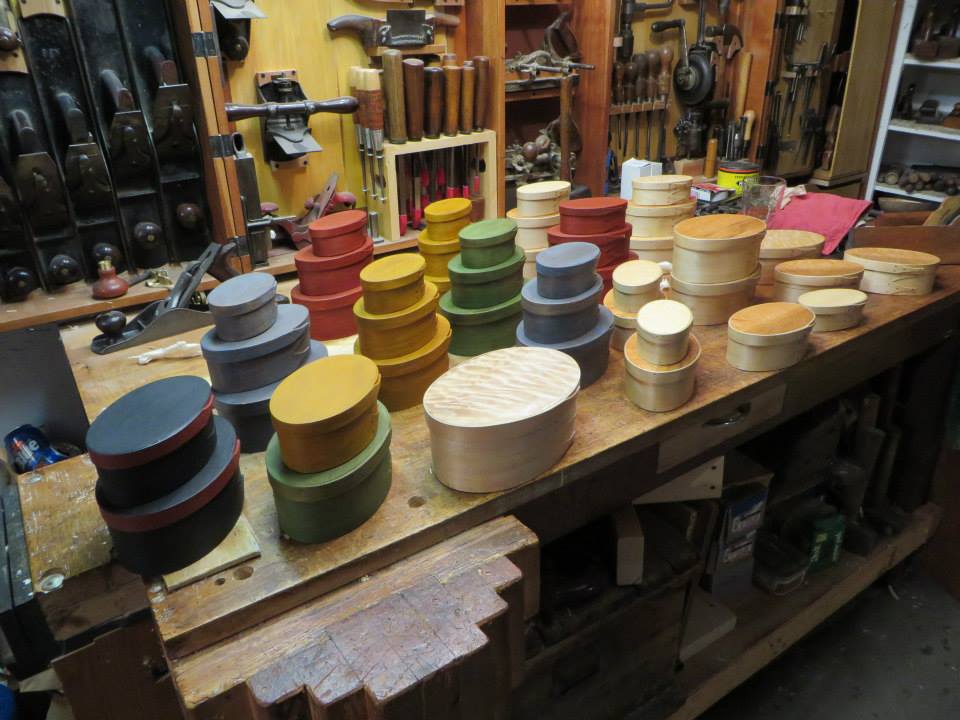
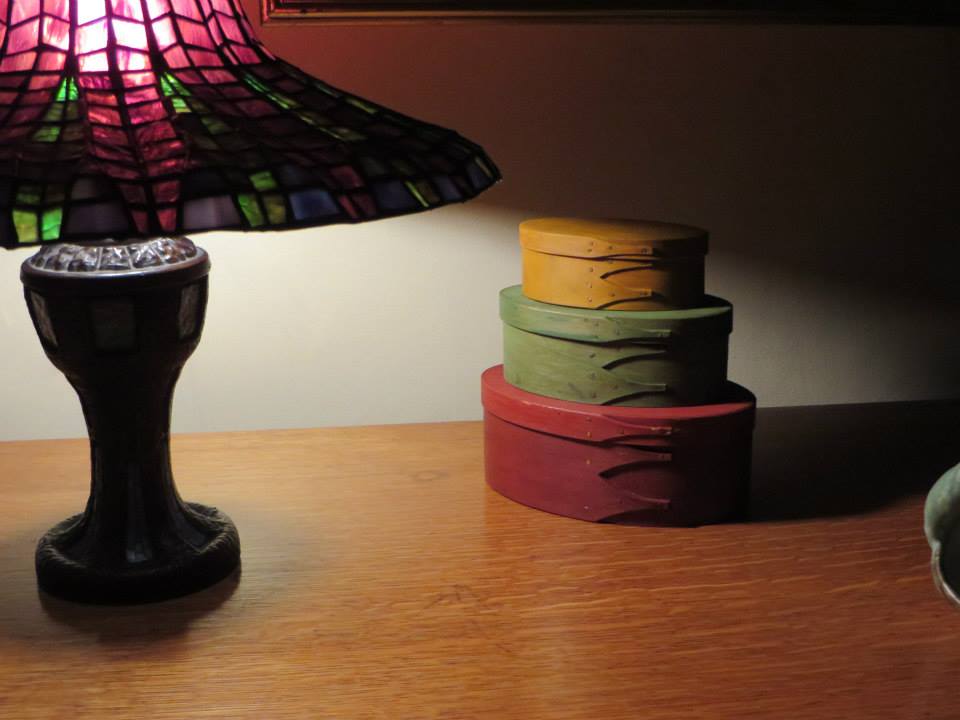
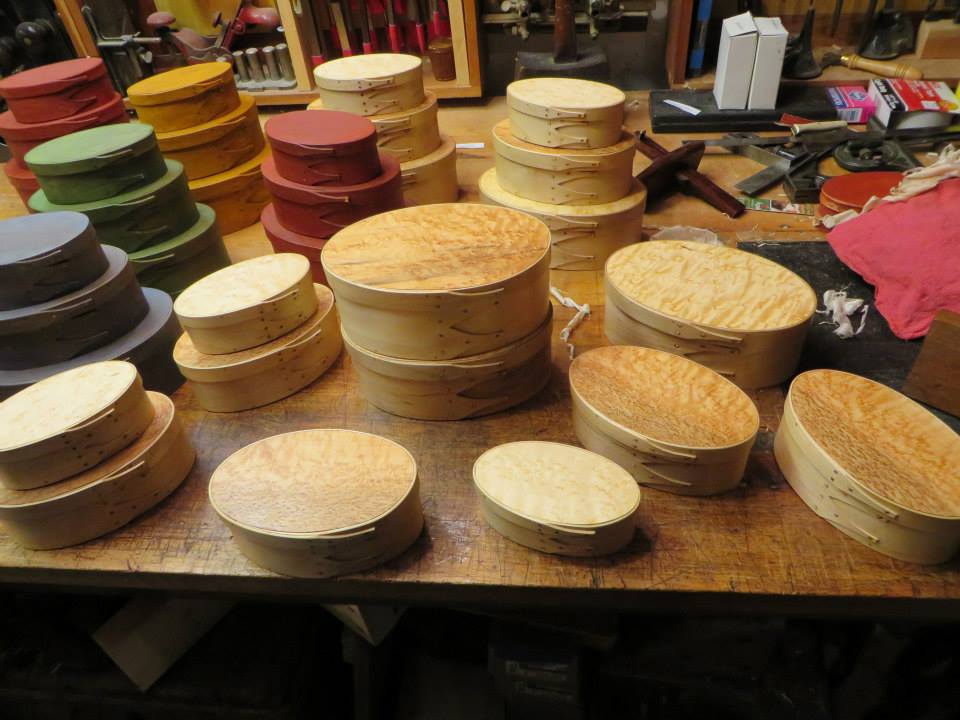